
Because the PID algorithm is going to run on a Real-Time based operating system with a fixed loop rate, right-click on the PID.vi and select SubVI Node Setup…. On the function palette, select the Control Design & Simulation->PID subpalette and drag and drop the PID.vi into the Control & Simulation Loop. Now double-click on the Transfer Function block to input the transfer function parameters.įigure 3. This places a Transfer Function block inside the Control & Simulation Loop. Create a Control & Simulation Loop.Īgain on the Simulation subpalette, select Continuous Linear Systems and click once on Transfer Function and once inside the Control & Simulation Loop you created previously. On the Functions Palette, select Control Design & Simulation->Simulation->Control & Simulation Loop then click and drag to size and create a Control & Simulation Loop.įigure 1. Start by opening the LabVIEW Development Environment and navigating to the Block Diagram. Your goal is to implement a PID algorithm that is going to run on a Real-Time controller with a loop rate of 1000 Hz (0.001 second period).
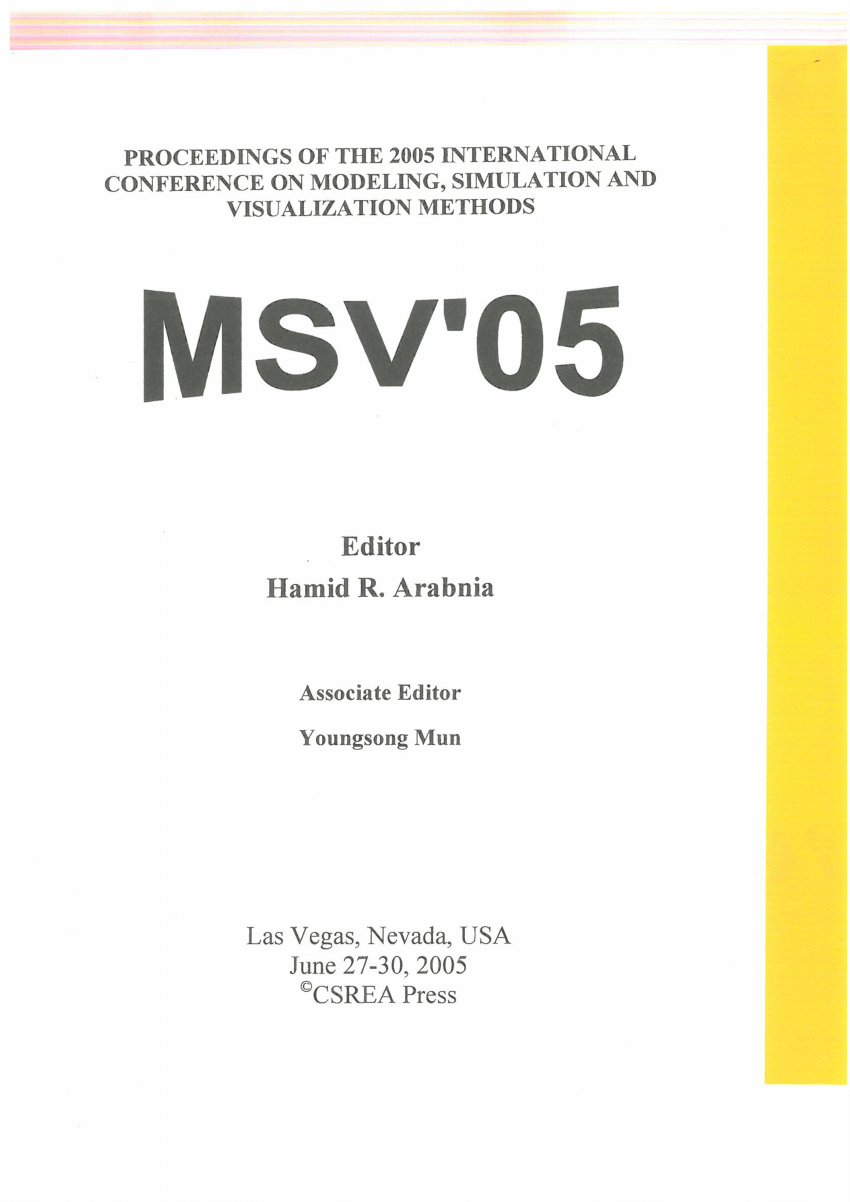
If you replace the numeric values, you get the following transfer function: For the sake of simplicity consider a basic transfer function for a DC motor where effects such as friction and disturbances are being considered:ī is the Friction Torque Constant (1.8E-6 N-m-s) REV Hub Interface Software - The REV Hub Interface is a beta software allowing for a direct connection from a REV Expansion Hub and its peripherals to a Windows PC.In this tutorial, we will design the velocity controller for a DC motor.Updating the Robot Controller Application.Updating Control Hub and Expansion Hub Firmware.Managing the Control Hub and Expansion Hub.The Control Hub and Expansion Hub are loaded with hardware interface options to enable driving motors and servos, interfacing with sensors, and communicating with other devices via several protocol options. The Control Hub and Expansion Hub are affordable hardware controllers that communicate with with each other and an Android Device Driver Station. Updating Multiple Devices with the USB-to-CAN Bridge.Building on the robust foundation of the original, SPARK MAX incorporates advanced brushed and brushless DC motor control in a small and easy-to-use package with PWM, CAN, and USB connectivity. SPARK MAX is the newest member of the SPARK Motor Controller family.
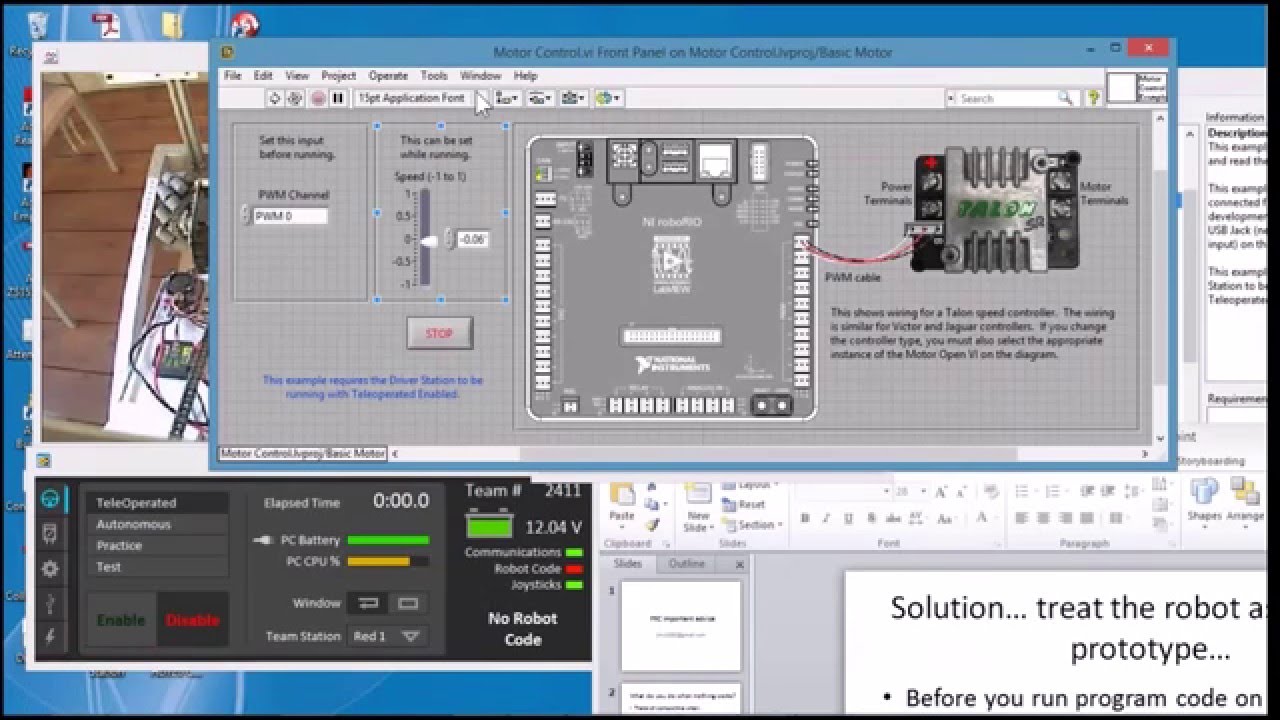
System Requirements and Installation Instructions.For a full list of supported products see the User's Manual. This software is used to configure, manage, and update products like the Control Hub, SPARK MAX, and Expansion Hub. The REV Hardware Client is software which allows for connection to REV Hardware devices and other supported devices via USB and WiFi. See the links below for more information. All Software Resources for REV Robotics products are now a part of.
